Inhalt
Das Ziel des Projektes ist die Reduzierung von Treibhausgasen und Steigerung der Energieeffizienz der gesamten Prozesskette. Dafür werden drei Bestandteile untersucht:
-
Schmelzprozess
Das Team erfoscht grüne Technologien, die beim energieintensiven Schmelzen von Magnesium eingesetzt werden können. Als alternativer Brennstoff soll dabei klimaneutraler Wasserstoff eingesetzt werden. Hierfür werden unter der Leitung von Prof. Krause am Institut für Wärmetechnik und Thermodynamik entsprechende Wasserstoffbrenner sowie Feuerungs- und Vorwärmtechnologien entwickelt. Des Weiteren untersuchen die Forschenden, wie die Wärmeübertragung an die Schmelze verbessert werden kann.
-
Verarbeitungsprozess
Die Forschenden entwickeln Technologien zur besseren Ausnutzung der Schmelzhitze während der weiteren Prozesse. Dafür schlägt das Team das ressourceneffiziente Gießwalzverfahren vor, bei dem aus dem flüssigen Magnesium schneller ein Halbzeug entsteht als bei herkömmlichen Verfahren. Verschiedene Umformschritte sollen dafür enger an den Gießwalzprozess gekoppelt werden, um auf dem Weg zum Halbzeug möglichst viel Wärmenergie aus der Gießhitze zu nutzen.
-
Legierung
Dritter Baustein des neuen Herstellungsprozesses ist der Einsatz einer besonders flexiblen Magnesiumlegierung, die bei niedrigen Temperaturen – und damit auch mit reduziertem Energiebedarf – in die gewünschte Form gebracht werden kann. Die Forschenden untersuchen dafür die calciumhaltige Magnesiumlegierung ZAX210.
Hintergrund
Im Sinne des European Green Deal spielt der Leichtbau als Querschnittsdisziplin eine entscheidende Rolle, um etwa im Transportwesen Ressourcen und Emissionen einzusparen. Das Verbundforschungsvorhaben CLEAN-Mag, welches im Rahmen des Förderprogrammes Technologie-Transfer-Programm Leichtbau (TTP Leichtbau) mit Mitteln des Bundesministeriums für Wirtschaft und Klimaschutz (BMWK) gefördert und vom Projektträger Jülich (PTJ) betreut wird, vereint 12 Partner aus Wissenschaft und Industrie. Weiterhin ist CLEAN-Mag Teil der Industrieinitiative NOCARBforging2050. Der Förderzeitraum des Projekts beträgt drei Jahre, wobei die beteiligten Institute der TU Bergakademie Freiberg mit 2,5 Millionen Euro gefördert werden.
Technologie-Matrix
Das Conform™-Verfahren (eingetragener Markenname der Firma BWE) oder auch das kontinuierliche Rotationsstrangpressen bietet die Möglichkeit, Halbzeuge unbegrenzter Länge herzustellen. Das Grundprinzip besteht darin, die beim konventionellen Strangpressen auftretenden unerwünschten Reibungskräfte zwischen Stempel und Rezipientenwand als treibende Kräfte zu nutzen. Dabei wird ein Draht durch eine umlaufende Nut eines Reibrades aufgenommen und in die Extrusionszone befördert. Das durch die Reibungshitze formbar gewordene Material kann anschließend direkt radial durch die dahinterliegende Matrize gepresst werden.
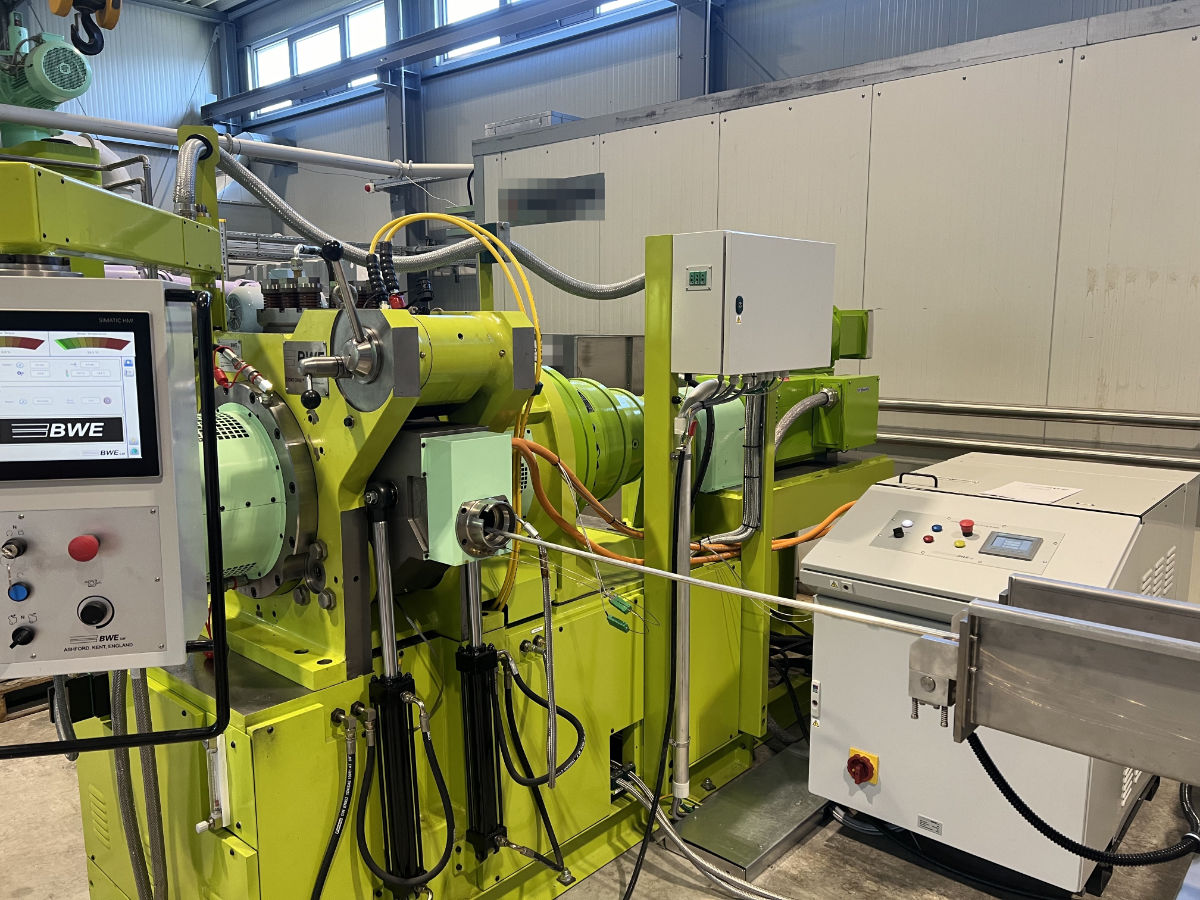
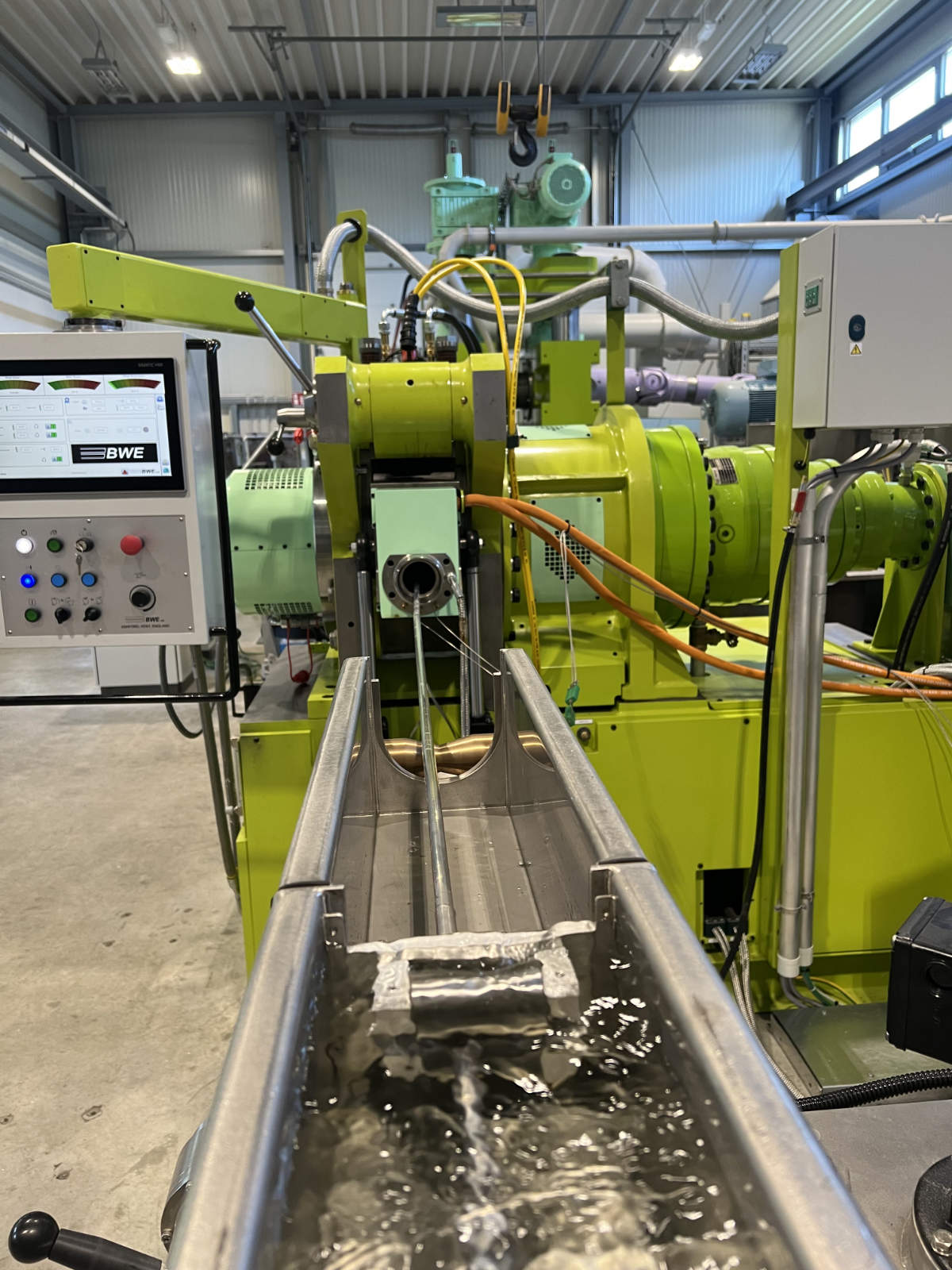
Die flammenlose Oxidation, kurz FLOX®, wurde von der Firma WS Wärmeprozesstechnik GmbH entdeckt. Mit dieser Technologie wird durch hohe Abgasrezirkulation eine Verbrennung ohne sichtbare Flamme erzeugt. Hierbei bildet sich ein homogenes Temperaturprofil im Ofen bzw. Strahlrohr aus und Temperaturspitzen wie an der Flammenfront bei der klassischen Verbrennung mit einer Flamme werden vermieden. Dadurch sinkt die thermische Stickoxidbildung auch bei hohen Luftvorwärmtemperaturen von Hocheffizienzbrennern drastisch. Des Weiteren wird aufgrund der Reduzierung der Temperaturgradienten die Lebensdauer der Bauteile, die mit der Verbrennung in Kontakt stehen, erhöht.
Diese Verbrennungstechnologie kommt zum Einsatz, wenn die Temperatur der rezirkulierenden Abgase die Selbstzündtemperatur überschreiten, üblicherweise bei Ofenraumtemperaturen über 850°C. Daher werden bei dieser Art der Verbrennung weder Zündung noch Flammenüberwachung benötigt. Darüber hinaus weist die FLOX®-Technologie eine hohe Brennstoffflexibilität auf, da keine Flamme in der Nähe des Brenners stabilisiert werden muss. Somit kann FLOX® auch bei den immer mehr in den Fokus rückenden grünen Gasen wie z.B. Wasserstoff und Ammoniak zum Einsatz kommen.
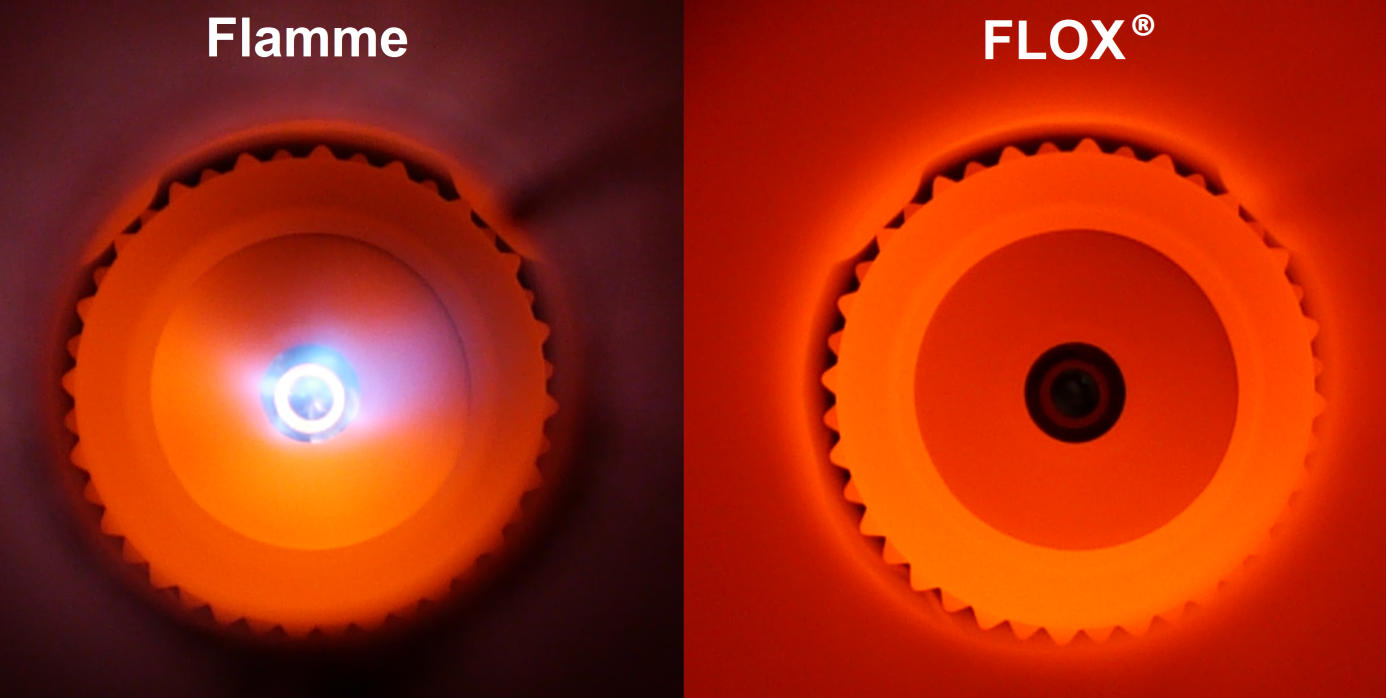
Die TUBAF betreibt eine weltweit einzigartige Pilotanlage zur Herstellung von Gießwalzband aus Magnesiumlegierungen. In Betrieb genommen im Jahr 2002 war die Anlage eine der ersten Gießwalzanlagen zur Herstellung von Magnesium-Blechen weltweit. Sie ermöglicht die Herstellung von Blechen mit verbesserten Eigenschaften und zu im Vergleich zum herkömmlichen Verfahren erheblich reduzierten Kosten. Im Jahr 2009 wurde die vorhandene Anlage zusätzlich um ein modernes Walzgerüst erweitert.
Die Pilotgießwalzanlage besteht aus zwei Komplexen. Der erste ermöglicht die Herstellung von Vorbändern mit einer Dicke von 3,5 bis 7 mm und einer Breite von maximal 780 mm. Im zweiten Komplex werden die Gießvorbänder in einem Quarto-Walzgerüst auf Enddicken bis minimal 0,5 mm fertiggewalzt.
Neben einer deutlich verbesserten Wirtschaftlichkeit und Produktivität zeichnet sich das Gießwalzverfahren durch ein verbessertes Fertigungsverhalten des erzeugten Materials aus, insbesondere eine verbesserte Walzbarkeit im Warmformgebungsprozess, gleichmäßigeren Eigenschaften über die Banddicke und -breite sowie superplastische Umformbarkeit.
Die Anlage besteht aus einem elektrisch beheizten Schmelzofen, welcher ein Fassungsvermögen von ca. 400 kg Magnesium aufweist. Die Schmelze wird anschließend in eine Headbox übertragen, von der aus das flüssige Metall in die Gießdüse und anschließend in den Walzspalt gelangt. Wird die Schmelze in das Ovalkaliber der zwei rotierenden, wassergekühlten Walzen vergossen, beginnt sie von außen nach innen zu erstarren und erfährt bereits eine erste Umformung. So werden kontinuierlich Drähte bzw. Stäbe mit einem Querschnitt von 9 x 20 mm hergestellt.
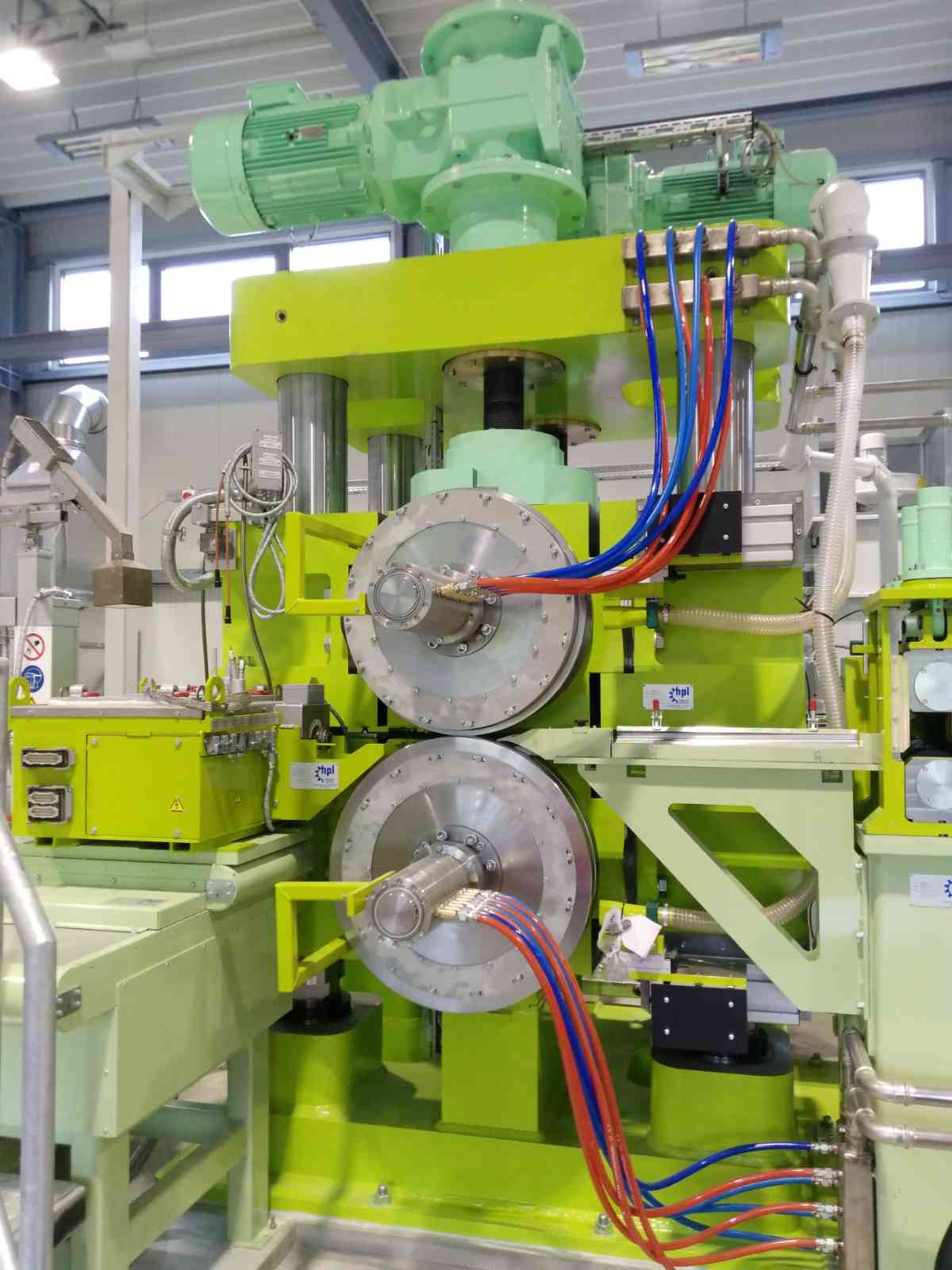
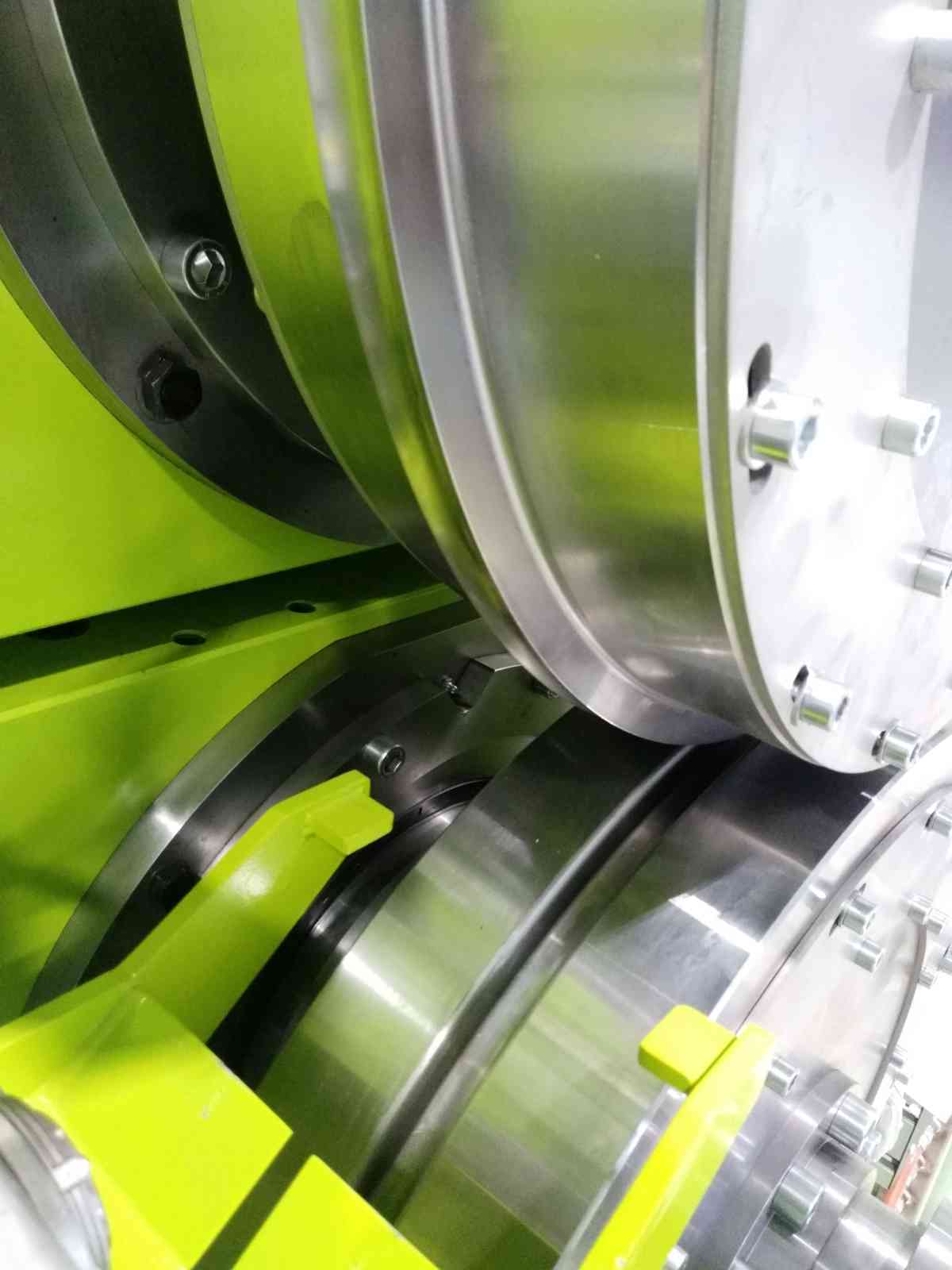
- JUBOcoat 1300: Dieses Verfahren wird für Zinkdruckguss und Aluminiumblech verwendet. Es bietet Cr(VI)-freie Konversion und ist als Phosphatierersatzmittel einsetzbar
- JUBOetch 3020: Ein Ätzverfahren mit geringem Fluoridgehalt, das in Kombination mit JUBOcoat 1300 für Konversionsbehandlungen von Wärmetauschern genutzt wird. Dieses Verfahren ermöglicht eine erhöhte Korrosionsschutzleistung
- JUBOcoat 1060: Eine chromfreie Beschichtung, die unter anderem für Zinkdruckguss und Aluminiumblech AlMg3 eingesetzt wird, um Korrosionsschutz zu bieten
- JUBOcoat 1742: Diese Beschichtung wird in Kombination mit PE-Pulverlack verwendet und bietet einen verbesserten Schutz gegen Korrosion, insbesondere für verzunderten Stahl
- JUBOetch 5xxx: Dieses Beizverfahren wird für Magnesium ME20 verwendet und ist Teil eines umfassenden Korrosionsschutzsystems, das auch JUBOcoat 1060 umfasst
Für die Forschungstätigkeit und Technologieentwicklung auf dem Gebiet der Langprodukte verfügt das Institut für Metallformung über eine offene, dreigerüstige Triostraße mit einer umfangreichen Kalibrierungsreihe zum Walzen von Rundstäben und -drähten mit unterschiedlichem Querschnitt. Neben der Herstellung von Vormaterialien für weitere Versuche, z.B. den Draht- oder Stangenzug, wird die Triostraße auch oftmals für Forschungen auf dem Gebiet von NE-Metallen und Sonderwerkstoffen eingesetzt. Zur Messung der prozesswichtigen Datensätze verfügt die Triotraße über eine Momentenmessung an den Antriebsspindeln, Kraftmessdosen für die Walzkraftmessung an allen drei Gerüsten. Für die Temperaturmessung ist die Anschlussmöglichkeit von mehreren Pyrometern an verschiedenen Messpunkten gegeben.
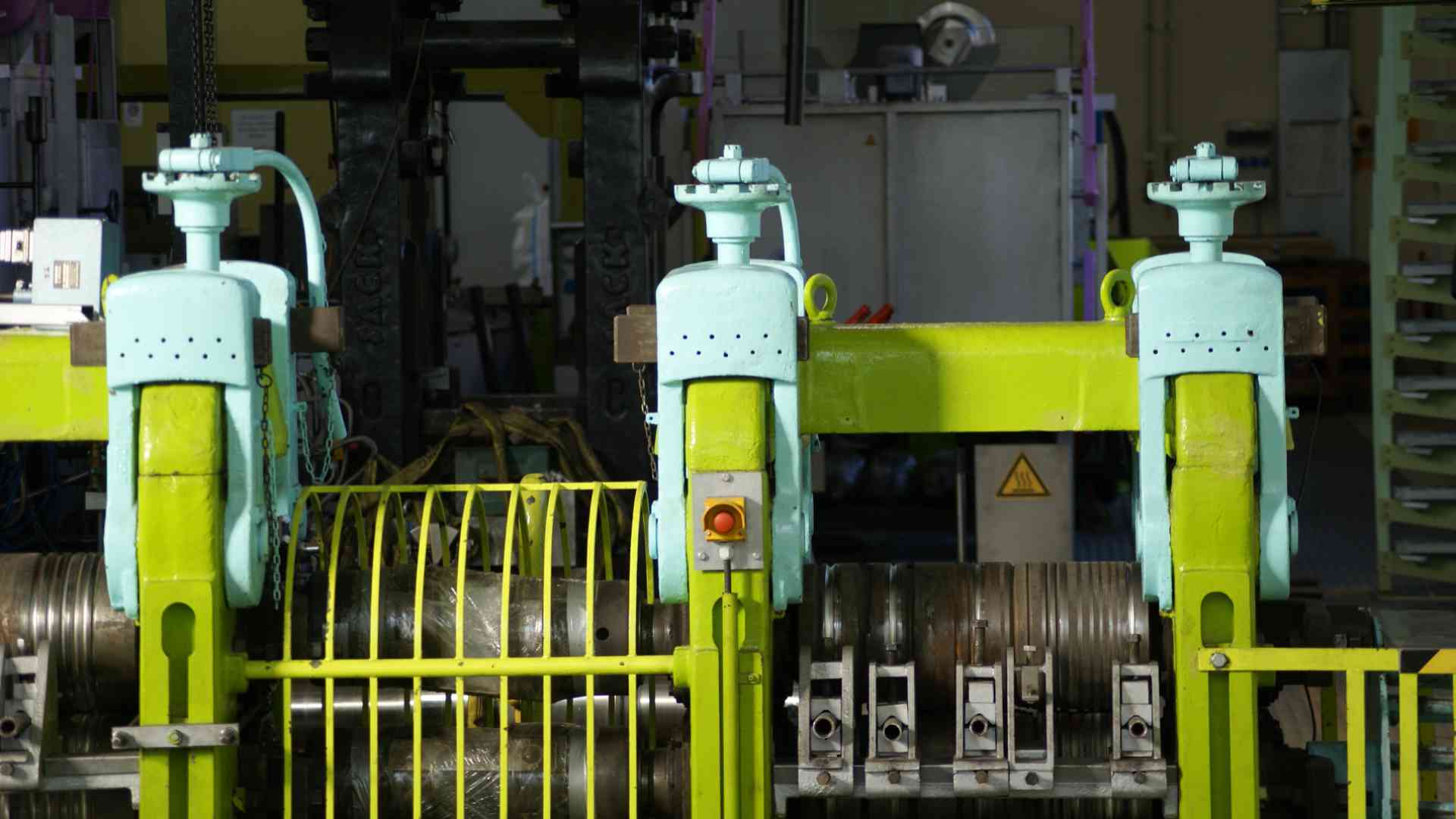
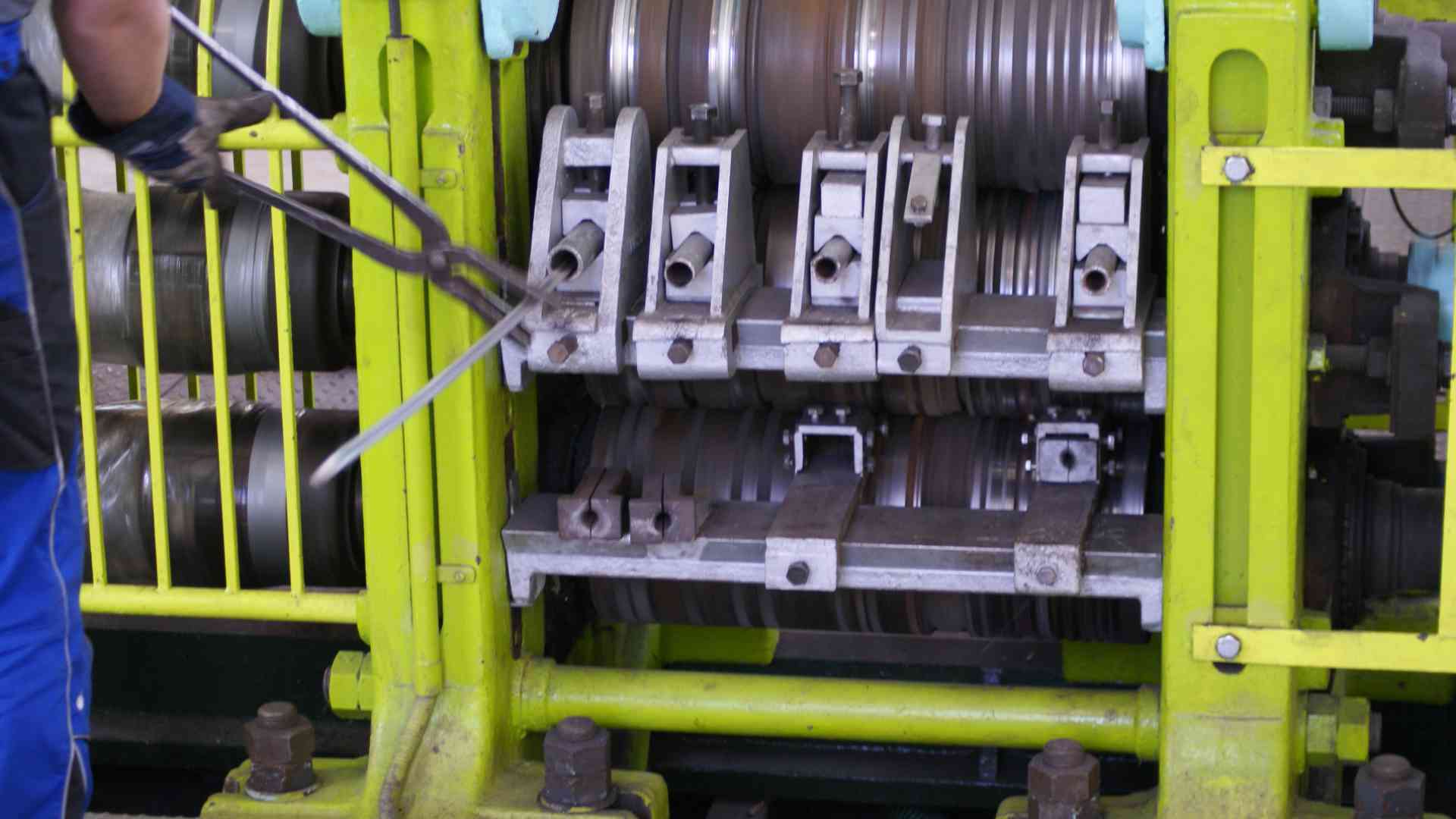