TAF Thermische Apparate Freiberg GmbH
Die TAF Thermische Apparate Freiberg GmbH, ein Unternehmen der Pörner Gruppe, ist Spezialist für Vergasungstechnologien sowie Entwickler und Anbieter von Sonderlösungen im Maschinen- und Anlagenbau, vor allem für höhere Prozesstemperaturen und/oder unter höheren Prozessdrücken.
Seit 2011 ist TAF Mitglied der Pörner Gruppe. Seit April 2022 firmiert sie als Tochterunternehmen der Pörner Ingenieurgesellschaft mbH - ein führendes Full-Service-Ingenieurunternehmen für verfahrenstechnischen Anlagenbau in Europa mit Sitz in Wien / Österreich.
Die TAF spezialisierte sich in den vergangenen Jahren auf die kundenspezifische Entwicklung und Fertigung von Pilot- und Forschungsanlagen mit Nachhaltigkeitsfaktor.
Ihr Know-how erschließt Kunden viele Vorteile:
- langjährige Kooperationen mit Universitäten und Forschungseinrichtungen eröffnen den Zugang zu neuesten wissenschaftlichen Forschungserkenntnissen
- ein funktionierendes Netzwerk mit regionalen Partnern ermöglicht die effiziente Realisierung von Gesamtanlagen
TAF ist damit in der Lage, innovative technologische Lösungen maßgeschneidert zu verwirklichen und Sonderkonstruktionen für bewährte und neuartige Prozesse umzusetzen.
Von der Idee über das Engineering bis zur Fertigung begleiten wir den gesamten Prozess, um sicherzustellen, dass unsere Kunden erstklassige Lösungen erhalten. Unsere Expertise erstreckt sich bis zur Inbetriebnahme, um sicherzustellen, dass die implementierten Technologien reibungslos funktionieren und den Anforderungen gerecht werden.
Als geprüfter Schweißfachbetrieb für die Herstellung und Instandsetzung von Dampfkesseln, Druckbehältern und Rohrleitungen verfügt das Unternehmen über alle notwendigen Zulassungen und Qualitätsprüfungsverfahren.
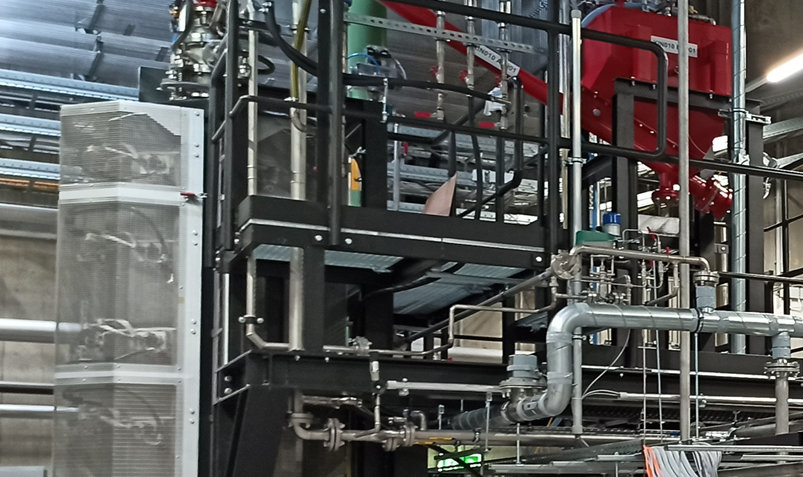
Gießwalzverfahren für Magnesium
Das Gießwalzverfahren für Magnesium ist eine fortschrittliche Methode zur Herstellung von Magnesiumblechen und -bändern. Dieser Prozess umfasst mehrere Schlüsselkomponenten, darunter das Ofengehäuse, zukünftig Wasserstoffbrenner anstelle herkömmlicher Erdgasbrenner, die Headbox, das Überführungsrohr und das Walzgerüst.
Ofengehäuse:
Das Ofengehäuse spielt eine zentrale Rolle im Gießwalzverfahren. Hier wird das Magnesium in einem Schmelzofen auf eine bestimmte Temperatur erhitzt, um es in einen flüssigen Zustand zu versetzen. Die präzise Kontrolle der Ofentemperatur ist entscheidend, um optimale Gießbedingungen zu gewährleisten.
Wasserstoffbrenner:
Die Verwendung von Wasserstoffbrennern ist vielfältig und hängt von den spezifischen Anforderungen des jeweiligen industriellen Prozesses ab. In metallurgischen Anwendungen sollen herkömliche Erdgasbrenner zukünftig auf Wasserstoff umgerüstet und ersetzt werden. Dabei spielt der Wasserstoffbrenner weiterhin eine wichtige Rolle bei der Schaffung einer schützenden Atmosphäre, um Oxidation zu verhindern und die Qualität der Metallprodukte zu verbessern.
Headbox:
Die Headbox ist für die gleichmäßige Verteilung des geschmolzenen Magnesiums verantwortlich, wenn es aus dem Ofen fließt. Diese Komponente spielt eine entscheidende Rolle bei der Steuerung der Gießgeschwindigkeit und -menge, um eine gleichmäßige Strömung auf die Walzanlage zu gewährleisten.
Transferrohr:
Das Transferrohr leitet das flüssige Magnesium vom Ofen zur Walzanlage. Es muss hitzebeständig und chemisch stabil sein, um den anspruchsvollen Bedingungen des Transports standzuhalten. Die präzise Auslegung des Transferrohrs ist entscheidend, um Verunreinigungen zu vermeiden und die Qualität des Endprodukts zu gewährleisten.
Walzgerüst:
Das Walzgerüst ist das Herzstück des Gießwalzverfahrens. Hier wird das flüssige Magnesium zu Blechen oder Bändern gewalzt. Die Walzwalzen sind präzise kalibriert, um die gewünschte Dicke und Oberflächenbeschaffenheit des Endprodukts zu erreichen. Die Temperaturkontrolle während des Walzprozesses ist ebenfalls entscheidend, um die mechanischen Eigenschaften des Magnesiums zu optimieren.
Insgesamt erfordert das Gießwalzverfahren für Magnesium eine sorgfältige Abstimmung und Kontrolle der verschiedenen Komponenten, angefangen vom Ofengehäuse bis zum Walzgerüst. Nur durch eine präzise Koordination dieser Elemente kann eine effiziente und qualitativ hochwertige Produktion von Magnesiumblechen und -bändern erreicht werden.
Teilvorhaben
Titel: Technische Entwicklung und Fertigung eines Schmelzezuführsystems für die Herstellung von Halbzeugen im Gießwalzverfahren
Die Entwicklung von Anlagen für das Prozessieren von Magnesiumschmelze in offenen Systemen stellt eine besondere Herausforderung dar aufgrund der besonderen Entzündungsneigung sowie die generelle Reaktivität, die jeweils legierungsabhängig ist und die es durch geeignete Maßnahmen zu kontrollieren gilt. TAF besitzt das notwendige Wissen und die Technologien, legierungsspezifisch sichere Fördersysteme zu entwickeln.
Kernarbeitsziele
Entwicklung eines Schmelzezuführungssystems für das Draht- und Bandgießwalzen mit dem Ziel einer stabilen Prozessführung und Sicherung einer hohen Produktqualität angepasst an die Verarbeitung von calciumhaltigen Mg-Legierungen.
Erfolgsaussichten
Die Firma TAF setzt auf aktuelle Entwicklungstrends im Bereich der Blechherstellung von kalziumhaltigen Mg-Knetlegierungen. Der steigende Bedarf dieser Legierungssysteme ergibt die Notwendigkeit, die Entwicklung großtechnischer Produktionssysteme voranzutreiben. Die damit einhergehende Forderung, kalziumhaltige Mg-Legierungen in ressourcenschonenden und energieeffizienten Produktionstechnologien zu etablieren, garantieren langfristige Erfolgsaussichten.